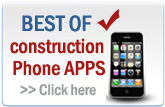
Ned Pelger's blog on construction, design and other weirdness. Email him at ned@constructionknowledge.net
Please help him win his readership competition against his son Lex at the Construction Phone Apps Blog
The Star Tribune in Minneapolis, MN recently reported that Target Corp has filed a federal racketeering lawsuit against LCH Pavement Consultants of Pearland, TX. Target claims LCH conspired with paving contractors in California, Wisconsin, Texas and Illinois to inflate prices, rig bids, fix prices, misrepresent work being done and distribute kickbacks.
Target hired LCH in 2009 and had them oversee about $100M US in repairs. The Star Tribune reports:
The suit alleges that LCH organized the participating paving companies in a scheme to divvy up the work on a territorial basis. LCH did this by denying some contractors a chance to bid, by getting some contractors to submit bids they knew were too high, and by fraudulently inflating legitimate, lower bids when it filed reports with Target, the suit says.
It says the defendant paving companies collaborated with one another by not submitting bids that would compete with another and reflect actual market pricing. Rather than overseeing the work, the suit says, LCH let the paving companies themselves, or a subcontractor, do the job and certify completion.
Of course, I have no way of knowing if the massive bid rigging fraud took place, but I doubt Target would endure the possibility of negative publicity without some fairly strong proof. When a CM breaches the trust of their Owner, the entire construction industry suffers.
As you look at how you do business, try to set up everything with as much transparency as possible. When one CM or contractor cheats, we all need to try harder to show that we don’t. The transparent processes actually will help your firm, not just to get work, but to protect against over-zealous types who will sacrifice ethical behavior for a quick profit.
We need to guard ourselves and our employees from getting into ethical quagmires. So look at your bidding and job costing processes, see if there’s a way to make them more transparent and stronger.
When I was a young foreman on a construction site, an old guy (younger than my age now) taught me how to do construction layout with an optic level. The first thing he explained was about bench-marks. To measure the relative elevation of different objects (I was laying out curbs…badly), I needed to be able to measure the height of my instrument off a known elevation, a bench-mark.
As I just completed the judging for the Engineering News Record Best Projects of 2011, I’ve been thinking about bench-marks. The most challenging aspect of judging the projects came from the inconsistency of the data presented. In our tele-conference yesterday, the other judges agreed.
Safety should be one of the easiest categories to bench-mark. Many years ago, OSHA tried to resolve that problem by requiring construction firms to measure their Experience Modifier (1.o being the average), their Lost Time Accident Rate and their Recordable Incident Rate. These measures should provide objective data to rate a firm’s safety effectiveness. Yet we’d see huge projects with Recordable Incident Rates of zero, that simply seemed impossible. To work millions of man-hours and not have any splinters in the fingers or strained muscles seems quite unlikely. It appears the numbers are being gamed or mis-reported somehow.
In another area, I’ve often noticed the lack of standards in measuring the costs of building projects. Some projects include everything from land to process equipment, while others only list the vertical building construction costs. I’m amazed how many times smart people don’t ask what is included in the stated costs. (Note to self: if you want to look smarter, make it a habit of asking what’s included and not included in prices when they are offered…learn to think critically about what any stated construction cost includes).
I’m a proponent of listing building project costs with the following simple break-outs:
I also like to always look at those costs as both a sf cost and a percentage of total project cost. These measures start helping you see trends, that help you understand the business better.
If you learn to present your projects in a clearer way, you’ll lose fewer projects to yahoos that confuse owners with scammy pricing. Remember, part of your job in selling a project is to educate the owner on the value you provide.
When I was a freshly minted engineer, I remember attending seminars taught by lawyers. They taught us about professional liability and the standard of care. Apparently, our designs weren’t held to the standard of perfection, but rather to the standard of the normal level of professional practice in the area we worked.
While that seemed a bit vague to me, it made sense that the real world dictates of limited time and money should allow that our work wouldn’t be perfect. As I hired architects and engineers over the years, I kept in mind that their design work would likely have some flaws. I tried to work as a team to catch mistakes prior to seeing them in the field, but have always understood that I wasn’t purchasing perfection.
Yesterday the presidential panel studying the BP Gulf oil spill produced a report favorable to BP, as reported in ENR. Fred Bartlit, the panel’s chief investigator, said, “To date we have not seen a single instance where a human being made a conscious decision to favor dollars over safety.”
The story in the media, of course, has focused on the failures. Two US Congressman sent a letter to BP in June stating, “The common feature of these five decisions is that they posed a trade-off between cost and well safety. Time after time, it appears that BP made decisions that increased the risk of a blowout to save the company time or expense.”
Those of us that actually produce things for a living, as opposed to those that count or critique that work, understand that every decision is a trade-off. We could always work to a higher standard of quality, of safety, of speed or of cost effectiveness. We just can’t do all of them at once.
It’s important for each of us to think about where we live on that continuum. Each of us needs to set our standards and understand what is acceptable and what’s not. Yes, the scenarios change, but principles shouldn’t.
If you want to be a leader in construction, you need to develop those principles about standards of quality, safety, schedule and cost. You need to decide what you believe. Finding the courage to stand up for those beliefs only happens if you actually know what you believe. If you don’t know what you believe, check out Joyful Living as a program that leads you through the process.
So don’t live your life terrified by litigation, you’ll never get anything done. Instead, decide on the standards you will live and work to, then strive to make them your legacy.
I got a call this morning that steel joists for a little church addition we are starting are 4″ too short. I thought this simply couldn’t be true. I had sent someone to field measure the existing condition, found it was 4″ longer span than showed on the architectural drawings, then emailed that info to everyone.
The steel shop drawings came through revised and I forwarded them to the Architect/Structural Engineer and the Project Superintendent for approval. Everything was approved and returned to the Steel Contractor for fabrication. No problem except that we all forgot to actually check the one thing we all knew was a change. I suppose we all assumed the guy before had made the change and didn’t go back to our files to verify. Or we just all went simultaneously brain dead.
Fortunately, we all work together as a team. Within minutes, I spoke with the Architect/Structural Engineer and we devised a solution that will fix the problem. I’m glad to work with group of people that cooperate and strive for fair solutions. The struggles of this crazy construction business become much more bearable when surrounded by an excellent team.
On the other hand, sometimes the Oops is so big that nothing could prepare you for it. Can you imagine building a project and coming in one morning and seeing this sinkhole that swallowed everything?
An article from Gizmodo verified that the photo was real and happened recently in Guatemala City during the tropical storm Agatha.
As I go through my daily living, I try to remember that small aggravations will happen (including my own mistakes) and that I need to forgive myself and others and keep getting things done. I also try to keep a floating feather of a thought in my head that a huge Oops can happen at any time. I hope I’m up to the task if it does.
My friend Randy Meyerhoffer just built some perfect Azak window boxes for a condo project we’re working on. Though a tad pricey, these window boxes set-off the entire facade. They are extraordinarily well made and beautiful. Randy lives his life dedicated to producing the highest quality possible. I don’t.
I appreciate high quality workmanship, I just think Owner’s should get to define the level of quality and cost they want, then obtain it. Randy sees this concept as the crappification of the world. Everything being done cheaper, not lasting as long, not as beautiful. I see it as a valid choice to save some cash and live with the results.
Wired magazine just did an excellent article The Good Enough Revolution: When Cheap and Simple is Just Fine which I strongly encourage you to read. They trace the trend that moderns often prize simplicity and use over high quality features. Think about how this affects what you design and what you build.
Too many times we install systems for Owners that never really work the way they envisioned. Many times the details for these systems get worked out on the jobsite. Over the years, I’ve become a stronger advocate for simplicity, telling Owner’s that what they think they want probably isn’t what they really want. While it takes some gumption to do that, the results are often worth it.
In everything we do, let’s think about what we really value. That’s the best way to determine if simplification can work. Begin by understanding that just because we can do or measure something, doesn’t mean we should.
I posted about some building structures falling down in China a few weeks ago and just got an interesting update (thanks Gravey). You may recall the photo, that has made it’s way around the internet, and dramatically shows the failure.
I castigated China in my post for likely not being forthcoming with an investigation and report, but it appears the failure is being studied and reports are being circulated.
“The investigation team’s report said that workers dug an underground garage on
one side of the building while on the other side earth was heaped up to 10 meters
high, which was apparently an error in construction, according to a report on
eastday.com, Shanghai’s official news website. “Any construction company with
common sense would not make such a mistake,” said an expert from the
investigation team.”
The construction company officials have been accused of incompetence and lacking common sense and put “under appropriate controls.”
The graphics below clearly show the sequence of events. It’s a good object lesson to remember to avoid rashness and step back and consider all the outcomes when making day to day decisions.
Since I’ve just finished a 10 part series on the construction industry as a career, I thought I’d celebrate some of the wonderful quality workmanship shown on the web. This first photo shows a recently completed bridge. That wavy concrete deck isn’t a result of some natural disaster, that’s just the way they formed and poured it.
The window shown below really doesn’t need an into.
“The curb machine was running and we were making great production and everything was going so well!”
I’m thinking perhaps the guy who had to explain the curb and manhole detail above jumped into a truck to get off the jobsite and found himself in the predicament below.
Hey, I’ve had bad days too. Hope you’re staying reasonably warm…or at least not complaining too much about it if you’re not.
Everything about India seems intense: the colors women wear, the smells both good and not, the spicy tastes and the use of the horn as a near constant tool for driving.
The modern high tech culture seems to have exploded within the traditional religious cultures. I saw a woman in Mumbai dressed in the traditional Muslim burka, nothing but her eyes showing through a slit in the black cloth. Then I look down and see her gold hi-heels. The huge Indian corporation TATA (that recently bought Jaguar from Ford) posts signs all over the country, selling steel, cell phones and lots more. Yet cows have the right of way in every traffic situation. Buddhist monks avoid swatting mosquitoes because all life is sacred, yet no 911 system exists. If you get hurt, you better have some resources and some friends to get emergency medical care.
I’ve stopped by several building sites and consistently notice the bamboo scaffolding, the random sapling trees used for floor shoring and concrete form tolerances that are, shall we say, quite generous.
The photos give a visual sense to my descriptions. We came across a fascinating enterprise as we exited a train. Over a million lunches get delivered each day from wives at home to their husbands working in Mumbai with a delivery error rate of one wrong delivery for every one million correct deliveries.
Think about what that means. One million wives make a hot lunch in the late morning all around the outskirts of Mumbai. Then a loose knit group of couriers pick up these lunches, carrying many at a time, hop on overloaded trains and buses and deliver the hot lunch each wife made to where her husband is working.
The couriers use a code system on top of the lunch pails. The photos below show some examples of the lunch pails, carriers and delivery code. Think about that level of quality…one million correct procedures for every fault. Now think about the construction project you are working on right now. Are there many errors on the project?
I’d say the average sized commercial building project has hundreds or thousands of errors. All the items that end up on a punch list, of course, but also many items that get covered up and aren’t quite right but nobody sees. If you’re honest and paying attention, I think you’ll agree that we have too many errors and failures on construction projects.
How do we improve? It’s complicated. Every stakeholder in the game has some responsibility. There is some “Do more and try harder” but there are also systematic changes that need to happen. What do you think needs to happen on your project?
By the way, I’ll be writing about this regularly because it’s a big item for which Construction Supervisors take most of the heat. Hopefully we can get some good discussions going about the theories and realities.